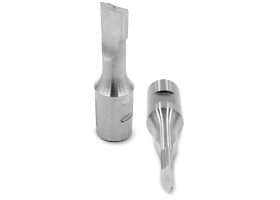
Six Lobe Punch Broaches
Created with two opposing lobes, Slater's Six Lobe Punch Broach Tools are used to produce hexalobular or Torx-type forms in tough applications on CNC lathes and mills. The Six Lobe punches are designed to conform with ISO 10664 and can be made in different materials and with coatings. These tools are especially beneficial when needing to create full form hexlobes and when broaching difficult-to-machine materials.
DIAMETER: .315" Shank Diameter
OVERALL LENGTH: 1.25”
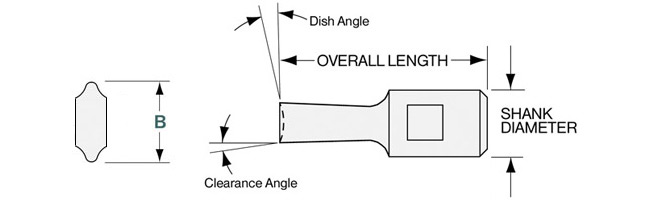
T Size | B | Part # |
---|---|---|
T6 Six Lobe Punch | 0.0703 | SP3-8-06 |
T8 Six Lobe Punch | 0.0954 | SP3-8-08 |
T10 Six Lobe Punch | 0.1123 | SP3-8-10 |
T15 Six Lobe Punch | 0.1333 | SP3-8-15 |
T20 Six Lobe Punch | 0.1563 | SP3-8-20 |
T25 Six Lobe Punch | 0.1798 | SP3-8-25 |
COATING OPTIONS
Titanium Nitride (TiN)
TiN is a gold colored PVD coating made of exceptionally hard ceramic material that improves lubricity, increases hardness and enhances abrasive wear resistance leading to increased broach tool life.
Titanium Carbonitride (TiCN)
TiCN is a purple-gray colored PVD coating formed by the addition of carbon to the TiN formula. The elevated hardness and low residual stress lead to excellent abrasive wear resistance. TiCN coating also increases lubricity of the broach and performs well under high load conditions. TiCN is commonly used in medical and aerospace applications broaching small forms in stainless steel and titanium materials.
Titanium Aluminum Nitride (TiAIN)
TiAlN is a dark gray colored PVD coating that can be used in high temperature conditions and for better lubricity. Harder than TiN, TiAlN has excellent abrasive wear resistance and is used successfully to broach many materials such as titanium, aluminum, stainless steels, and alloy steels.
MATERIAL OPTIONS
M2 High Speed Steel
M2 is a molybdenum based high speed steel that is characterized by abrasion resistance, toughness and good red hardness. Slater Tools' hardened M2 broaches have an ideal balance of bending strength, toughness and wear resistance. M2 is used in a wide range of rotary broaching applications and is suitable for any broachable material.
PM M4 High Speed Steel
PM M4 is a molybdenum-tungsten high speed steel, which is produced with a very consistent and refined structure. This structure gives PM M4 broaches several enhanced properties including improved toughness and better wear resistance. This material is good for stainless steel and titanium applications for decreased wear.
T15 High Speed Steel
PMT15 is a high-carbon tungsten-cobalt-vanadium high speed steel, composed of very fine grain structures. T15 has excellent red hardness and abrasion resistance. Like the PM M4, the structure of PM T15 broaches improves toughness and is a good choice for improving overall broach tool life.
OTHER CUSTOM OPTIONS
- Custom overall tool lengths
- Custom cut lengths
- Special dimensions
- Vent holes
- Alterations to flat on broach tool shank
Index Punch Broaching Part Preparation
Pre-Drill Hole Diameter:
- A pre-drill hole is required for index punch broaching.
- The pre-drill hole must be at least equal to the minor diameter of the finished form. It is strongly recommended to open the hole diameter larger than the minor diameter.
Pre-Drill Hole Depth:
- The depth of the pre-drill hole must be greater than the broaching depth to allow for chips to accumulate and avoid excess packing.
- If chips must be removed after broaching, it can be done with a drill or boring tool. A recess at the bottom of the pre-drill will allow the chips to break cleanly. The recess diameter should be larger than the major diameter of the broach.
- It is recommended to have a pre-drill depth of 1.75 x depth of broached area.
Lead Chamfer:
- A 45° lead chamfer must be provided for successful index punch broaching, going from the major diameter to the minor diameter of the form.
Machine Setup Parameters
- Position broach tool a sufficient distance away from face of workpiece to allow for acceleration to full cutting speed
- Use machine’s peck mode and feed to the desired depth. Alternatively, program the machine to rapid in and then retract the tool in .005 increments
- Spindle lock or ability to program lock is required
ORDER DIRECT
- Upload Purchase Order Here
- Call: (586) 465-5000
- Fax: (586) 465-3030